Introduction
New technology in the New Zealand construction industry
In the ever-evolving New Zealand construction industry, new technology is transforming the way we build.
Technology has become crucial in this field, significantly impacting efficiency, safety, and overall project management.
Technological advancements have revolutionized traditional construction practices, allowing for faster and more precise project execution.
With tools like Building Information Modeling (BIM), architects and engineers can now create digital representations of structures, enabling better visualization and collaboration among stakeholders.
Moreover, sophisticated software and hardware solutions have enhanced various aspects of construction management.
Project scheduling and cost estimation software streamline operations, minimize errors, and improve resource allocation.
Drones equipped with high-resolution cameras provide real-time aerial imagery, facilitating site inspections and progress monitoring.
importance and impact of technology in this field
The adoption of technology in the construction industry also improves safety and reduces risks.
Wearable devices and sensors can monitor workers’ health and provide early warnings of potential hazards, preventing accidents.
Automated machinery and robotics reduce manual labor, minimizing human exposure to dangerous tasks.
Furthermore, sustainability is a top priority in today’s construction practices, and technology plays a vital role in achieving this.
Innovations like 3D printing allow for the creation of eco-friendly materials and structures, reducing waste and carbon footprint.
Smart energy management systems optimize resource usage, making buildings more energy-efficient and environmentally friendly.
In review, technology has become an indispensable part of the New Zealand construction industry. It has revolutionized how projects are envisioned, managed, and executed.
By embracing new technology, the industry can continue to thrive, delivering safer, more efficient, and environmentally conscious construction projects.
New Tech in NZ Construction Industry: Drones in Construction
In recent years, the use of drones in the construction industry has revolutionized various processes, specifically in surveying and inspection purposes.
Companies in New Zealand have embraced this innovative technology, reaping numerous benefits such as cost-efficiency and improved safety.
Benefits of Using Drones in Construction
- Cost-efficiency: Drones significantly reduce expenses by eliminating the need for traditional surveying methods.
- Improved Safety: With drones, workers can avoid risky situations by gathering data from otherwise inaccessible areas.
- Enhanced Accuracy: Drones provide precise measurements and data, minimizing human errors in surveying and inspection.
- Time-saving: Using drones reduces the time it takes to complete surveys and inspections, enhancing project timelines.
Examples of Drone Adoption in New Zealand
New Zealand construction companies have embraced drone technology, capitalizing on its potential to streamline operations and enhance overall efficiency.
- Fletcher Construction: As a leading construction company, Fletcher has integrated drones into their surveying and site inspection processes. This has allowed them to gather accurate data efficiently.
- Downer Group: Downer, one of New Zealand’s largest construction companies, utilizes drones for aerial inspections of large-scale projects, ensuring improved safety and quality control.
- Hawkins Construction: Hawkins Construction employs drones to conduct site surveys and monitor progress. This facilitates better project management and allows for early identification of any issues.
These are just a few examples of how drones have been adopted in the New Zealand construction industry, showcasing the diverse applications and advantages they offer.
Furthermore, the use of drones in construction goes beyond surveying and inspections.
They can also aid in monitoring construction sites, capturing aerial imagery for marketing purposes, and even assisting in the delivery of materials.
The versatility and potential for innovation with drone technology are vast.
As drones continue to evolve, the construction industry in New Zealand will undoubtedly explore more opportunities to integrate this technology into their processes.
Therefore, the use of drones in the New Zealand construction industry has proven to be a game-changer.
From cost-efficiency and improved safety to enhanced accuracy and time-saving, the benefits are undeniable.
Construction companies such as Fletcher, Downer, and Hawkins have already embraced drones, setting a precedent for others to follow.
As the technology continues to advance, we can expect even more exciting developments in the near future.
Building Information Modeling (BIM)
Building Information Modeling (BIM) is a revolutionary technology that has transformed the construction process in New Zealand.
BIM goes beyond 3D modeling, as it creates a digital representation of a building’s physical and functional characteristics.
This model serves as a shared knowledge resource that allows collaboration between different stakeholders throughout the entire project lifecycle.
Advantages of Using BIM
The implementation of BIM technology comes with numerous benefits for the construction industry in New Zealand.
- Enhanced Collaboration: BIM enables real-time collaboration among architects, engineers, contractors, and other project stakeholders.
- Improved Efficiency: BIM eliminates the need for multiple iterations as changes made to one aspect of the model are automatically reflected in all related components.
- Reduced Errors: By utilizing BIM, potential clashes and conflicts in design can be detected early in the process, leading to reduced errors and costly rework.
- Better Visualization: BIM allows stakeholders to visualize the building in a more detailed way, providing a more accurate representation of the final project outcome.
- Cost and Time Savings: BIM enables more accurate estimations of project costs and schedules, resulting in significant savings for construction firms.
New Zealand Construction Firms Implementing BIM Technology
New Zealand construction firms have embraced BIM technology, recognizing its ability to improve efficiency and streamline construction processes.
Personalized Career Consulting
Unlock your potential with expert career advice tailored to your goals. Get personalized guidance and actionable steps toward your dream career in New Zealand.
Get Started- Fletcher Construction: As one of the largest construction companies in New Zealand, Fletcher Construction has successfully integrated BIM into its workflow.
BIM has enabled effective coordination between different teams, leading to a reduction in clashes and improved project coordination. - Hawkins Construction: Hawkins Construction has also implemented BIM technology across its projects.
By leveraging BIM, the company has enhanced collaboration between stakeholders, resulting in a streamlined construction process and improved project outcomes. - Arrow International: Arrow International has embraced BIM technology to streamline its construction operations.
By utilizing BIM, the company has improved communication, reduced errors, and achieved better project coordination. - Mainzeal: Mainzeal has recognized the potential of BIM technology in the construction industry.
They have implemented BIM to enhance collaboration and improve efficiency, resulting in successful project delivery.
Generally, Building Information Modeling (BIM) has revolutionized the construction industry in New Zealand.
Its advantages, such as enhanced collaboration and reduced errors, have led to increased efficiency and improved project outcomes.
Construction firms, including Fletcher Construction, Hawkins Construction, Arrow International, and Mainzeal, have successfully implemented BIM technology to reap its numerous benefits.
With the continued adoption of BIM, the construction industry in New Zealand is set to further evolve and thrive.
Read: Residential vs Commercial: NZ Electrician Roles
Virtual Reality (VR) and Augmented Reality (AR)
Virtual Reality (VR) and Augmented Reality (AR) are two innovative technologies that are revolutionizing the construction industry.
These immersive technologies offer new possibilities and transform the way projects are designed, visualized, and managed.
How VR and AR are transforming the construction industry
- VR and AR enable architects and designers to create virtual models, allowing stakeholders to visualize and experience the final product before construction begins.
- These technologies provide a realistic and interactive environment, allowing users to walk through buildings, explore different design options, and make informed decisions.
- VR and AR also enhance communication and collaboration among project teams, enabling seamless coordination and reducing costly errors.
- Construction workers can use AR headsets to overlay digital information onto the physical environment, improving accuracy and efficiency in tasks such as equipment placement and installation.
- These technologies also enhance safety by providing workers with real-time information, alerts, and training simulations, minimizing the risk of accidents and injuries.
Applications of VR and AR in design visualization, training, and project management
- Design Visualization: VR and AR allow architects and clients to envision the final design in a realistic and immersive manner, facilitating better design decisions.
- Training: VR and AR provide a safe and controlled environment for construction workers to practice complex tasks, improving their skills and reducing training costs.
- Project Management: VR and AR enable project managers to track progress, visualize project timelines, and identify potential issues before they occur, leading to more efficient project delivery.
Successful use cases of VR and AR technology in New Zealand construction projects
- The Christchurch Town Hall restoration project utilized VR to allow stakeholders to virtually explore the revamped building, resulting in increased stakeholder engagement and satisfaction.
- VR was employed in the construction of the International Convention Centre in Auckland, enabling designers and contractors to identify clashes between building systems early, optimizing coordination and reducing rework.
- AR technology was used in the development of the Northern Pathway project in Wellington, allowing designers to overlay proposed changes onto the existing landscape, facilitating informed decision-making.
These successful use cases demonstrate the potential of VR and AR to improve project outcomes, enhance collaboration, and streamline construction processes in the New Zealand construction industry.
Read: The Impact of Technology on NZ Electricians
Prefabrication and Modular Construction in the New Zealand Construction Industry
Prefabrication and modular construction methods are gaining increasing popularity in the construction industry in New Zealand.
These innovative techniques offer numerous benefits, including accelerated construction timelines and improved quality control.
Let’s explore why they are becoming so widely adopted and provide examples of successful projects in the country.
Growing Popularity of Prefabrication and Modular Construction
- One of the main reasons for the growing popularity of prefabrication and modular construction methods in New Zealand is their ability to significantly reduce project timelines.
- By constructing building components off-site in a controlled environment, construction time can be greatly accelerated.
- Traditional on-site construction processes often face delays due to weather conditions and other unforeseen circumstances, which can be minimized through off-site manufacturing.
- Prefabricated components can be manufactured simultaneously while site preparation and foundation work are being completed, allowing for a streamlined construction process.
- Furthermore, prefabrication and modular construction maximize efficiency by reducing material waste and optimizing the use of resources.
Benefits of Prefabrication and Modular Construction Techniques
- Accelerated Construction Timelines: Prefabrication enables faster completion of projects, reducing overall construction time by up to 50%.
- Cost Savings: Due to the faster completion time, labor costs can be significantly reduced, resulting in overall cost savings for clients and developers.
- Improved Quality Control: Prefabrication allows for precise manufacturing and rigorous quality control checks, resulting in higher quality buildings and structures.
- Minimized Environmental Impact: These techniques minimize construction waste and emissions, making them more eco-friendly compared to traditional construction methods.
- Flexibility and Adaptability: Prefabricated components can be easily modified or expanded, offering adaptability to changing needs over time.
Examples of Successful Projects
- The Wynyard Quarter Innovation Precinct in Auckland utilized prefabrication techniques to construct several buildings, including the popular Generator building.
- The innovative exemplar for affordable housing, The Parnell development, relied on modular construction to deliver high-quality homes efficiently.
- The Christchurch Town Hall restoration project successfully incorporated prefabrication methods, allowing for swift post-earthquake reconstruction.
- Another noteworthy project is the Brockworth Place office building in Wellington, which was constructed using modular components, saving time and costs.
- The Nelson Marlborough Institute of Technology’s Arts and Media Building showcased the benefits of prefabrication, ensuring a swift and precise construction process.
These examples demonstrate the success and effectiveness of prefabrication and modular construction methods in New Zealand.
As the industry continues to adopt these techniques, we can expect to see further advancements in construction efficiency, quality, and sustainability.
Read: Apprenticeships in Electrical Work: NZ Focus
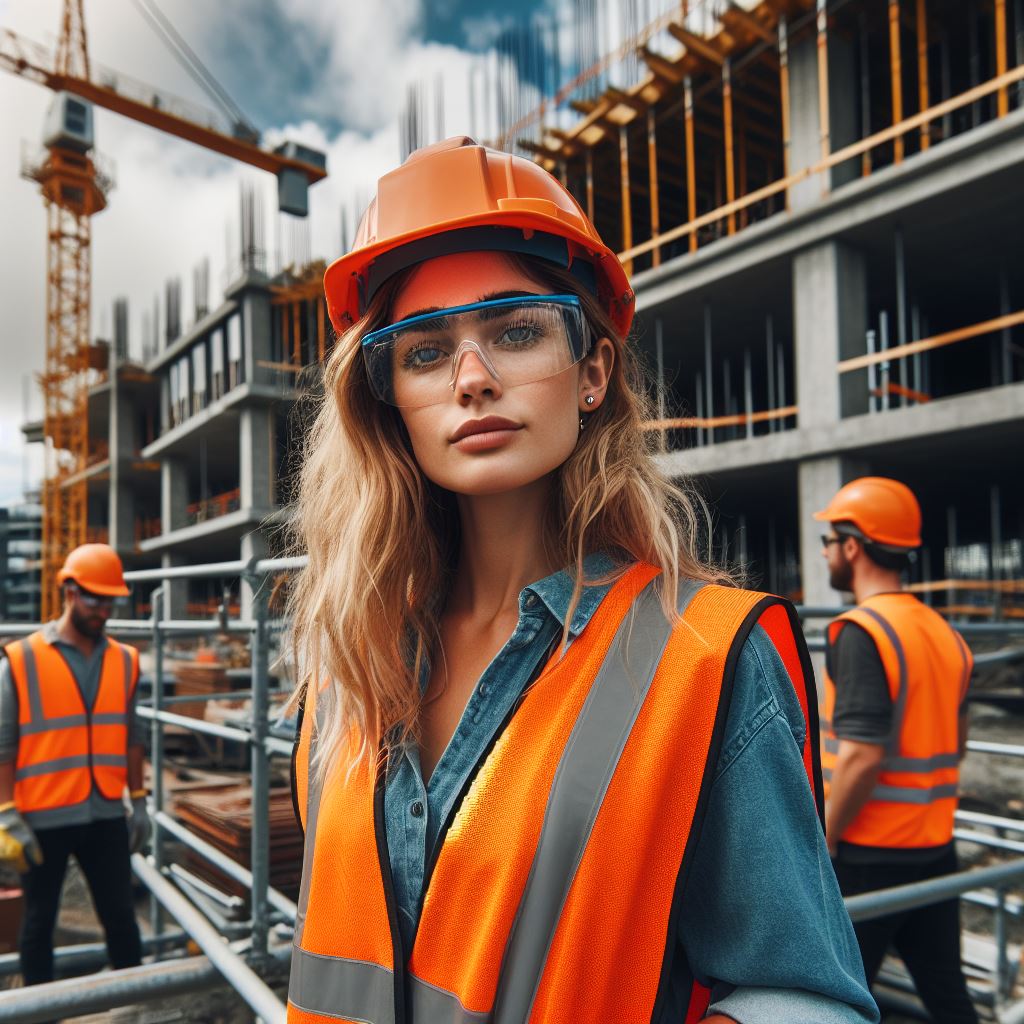
Robotics and automation
The role of robotics and automation in New Zealand’s construction industry
In recent years, New Zealand’s construction industry has witnessed significant developments in the field of robotics and automation.
These technologies are revolutionizing the way construction projects are carried out and have the potential to significantly impact productivity and labor dynamics in the sector.
Robots are increasingly being utilized in various tasks within the construction industry, including bricklaying, demolition, and material handling.
By automating these tasks, construction companies can save time, reduce costs, and improve overall efficiency.
How robotics are being used for tasks such as bricklaying, demolition, and material handling
One area where robotics has gained considerable traction is bricklaying. Bricklaying robots are capable of laying bricks at a much faster pace than human workers, significantly reducing construction time.
These robots are programmed to precisely place bricks in the desired pattern, ensuring accurate and high-quality results.
Demolition is another area where robots have proven to be highly effective. Demolition robots can easily navigate through hazardous environments and remove structures without risking human lives.
With their precision and ability to work in tight spaces, these robots ensure the safe and efficient demolition of buildings.
Material handling is a vital aspect of construction projects, and robotics has greatly enhanced this process.
Automated systems are now available for lifting and transporting heavy materials, reducing the strain on human workers and minimizing the risk of injuries.
This technology not only improves productivity but also ensures a safer work environment.
The potential impact of robotics and automation on productivity and labor dynamics in the sector
The potential impact of robotics and automation on productivity and labor dynamics in the construction industry is immense.
By taking over repetitive and labor-intensive tasks, robots free up human workers to focus on more complex and creative aspects of construction projects.
Transform Your Career with a Professional CV and Cover Letter
Stand out to employers with an ATS-optimized resume and tailored cover letter designed to match your dream role. Let us craft your job application materials for success!
Get StartedIncreased productivity resulting from automation can also lead to shorter project timelines and improved cost-effectiveness.
Companies can complete projects at a faster rate, enhancing their competitiveness in the market.
Additionally, with robots performing tasks with precision and accuracy, the quality of construction is also likely to improve.
However, the introduction of robotics and automation does raise concern about potential job losses in the industry.
As robots become more capable of performing tasks traditionally done by humans, there is a possibility of reduced demand for manual labor.
This could impact the workforce and result in job reallocation or retraining.
Despite these concerns, the overall impact of robotics and automation in the construction industry is expected to be positive.
The sector can benefit from increased efficiency, improved safety, and enhanced capabilities.
Companies that embrace and integrate these technologies are likely to gain a competitive advantage and contribute to the growth and development of New Zealand’s construction industry.
In essence, robotics and automation are playing an increasingly significant role in New Zealand’s construction industry.
From bricklaying and demolition to material handling, robots are transforming the way construction projects are carried out.
While there may be concerns about job displacement, the potential benefits in terms of productivity, efficiency, and safety are substantial.
By embracing these technologies, the sector can achieve higher levels of success and contribute to the advancement of the industry as a whole.
Read: Women in Electrical Trades: NZ’s Growing Trend
Conclusion
Various new technologies are being adopted in the New Zealand construction industry
In closing, the New Zealand construction industry has been quick to embrace and implement new technologies.
We have seen the adoption of advanced 3D printing and drone technology, as well as the use of Building Information Modeling (BIM) and augmented reality in design and construction processes.
Benefits and opportunities these technologies bring to the sector
These technologies have brought numerous benefits and opportunities to the sector. 3D printing has allowed for efficient and cost-effective creation of complex architectural designs.
Drones have improved safety and monitoring on construction sites. BIM has enhanced collaboration and communication among project stakeholders.
Augmented reality has revolutionized the way designs are visualized and presented to clients.
Final thoughts on the future of technology in construction and its potential to reshape the industry
Looking ahead, the future of technology in construction seems promising. As automation and artificial intelligence continue to advance, we can expect even greater efficiency and productivity in the industry.
Robotics may take over hazardous tasks, reducing the risk to human workers. Blockchain technology may streamline supply chain management and improve transparency.
However, it is important to emphasize that while technology brings opportunities, it also poses challenges.
The industry must adapt to new ways of working and ensure that workers have the necessary skills to operate and manage these technologies effectively.
Overall, the integration of new technologies in the New Zealand construction industry has the potential to reshape the sector.
It is an exciting time for the industry as we witness the transformative power of technology.
With continued innovation and adoption, we can expect a more sustainable, efficient, and dynamic construction industry in the future.