Introduction
The supply chain crisis refers to disruptions that hinder the flow of goods and materials, causing substantial impact on New Zealand.
Effective crisis management is crucial to ensure smooth supply chain operations.
In today’s globalized world, supply chains are increasingly complex and vulnerable to various risks and disruptions.
New Zealand, being highly dependent on imports and exports, is particularly susceptible to supply chain crises.
These crises can arise from natural disasters, economic crises, geopolitical conflicts, or even pandemics like the recent Covid-19 outbreak.
When a crisis strikes, it can lead to severe disruptions in the supply chain, resulting in scarcity of goods, delayed deliveries, increased costs, and overall economic instability.
That is why effective crisis management is crucial. It enables companies to minimize the impact of a crisis and quickly restore normal operations.
By having robust risk management strategies, companies can proactively identify potential disruptions and develop contingency plans to mitigate risks.
Furthermore, crisis management helps in maintaining customer satisfaction.
By promptly communicating with customers and ensuring transparency throughout the crisis period, companies can build trust and loyalty.
This not only helps in retaining existing customers but also attracts new ones.
Effective crisis management is also essential in protecting the reputation of companies.
Companies that handle crises well, take responsibility, and show resilience, often gain respect and trust from stakeholders.
On the other hand, companies that fail to effectively manage crises may face reputational damage and long-term consequences.
In essence, the supply chain crisis can significantly impact New Zealand.
Personalized Career Consulting
Unlock your potential with expert career advice tailored to your goals. Get personalized guidance and actionable steps toward your dream career in New Zealand.
Get StartedHence, effective crisis management is vital to minimize disruptions, maintain customer satisfaction, and protect the reputation of companies.
By being prepared and responsive, companies can navigate through crises and ensure the smooth flow of goods and materials.
Overview of Supply Chain Crisis Management
Definition and meaning of supply chain crisis management
Supply chain crisis management is the process of identifying, evaluating, and responding to potential disruptions within a supply chain network.
It involves developing strategies to mitigate risks and minimize the negative impact of crises on operations.
Key components of effective crisis management in supply chain operations
Effective crisis management in supply chain operations requires a holistic approach.
Here are some key components to consider:
1. Risk Assessment
Identify and assess potential risks that may disrupt the supply chain, such as natural disasters, pandemics, political instability, or technological failures.
Prioritize risks based on their likelihood and potential impact on the operations.
2. Business Continuity Planning
Develop a comprehensive business continuity plan to ensure the continuous flow of goods and services during a crisis.
This plan should include alternative sourcing options, backup suppliers, and redundant logistics networks.
3. Communication and Collaboration
Establish effective communication channels with stakeholders, including suppliers, customers, and government agencies.
Collaborate closely with these partners to share information, coordinate response efforts, and address challenges collectively.
4. Supply Chain Visibility
Implement technologies and systems that provide real-time visibility into the supply chain network.
This enables proactive monitoring of inventory levels, demand patterns, and logistics activities, allowing for timely identification of potential disruptions.
Transform Your Career with a Professional CV and Cover Letter
Stand out to employers with an ATS-optimized resume and tailored cover letter designed to match your dream role. Let us craft your job application materials for success!
Get Started5. Diversification and Redundancy
Diversify supplier and logistics networks to minimize reliance on a single source or route.
This helps reduce the impact of localized disruptions and ensures alternative options are available to maintain the flow of goods.
6. Continuous Monitoring and Evaluation
Regularly monitor the supply chain performance, identify warning signs or early indicators of potential crises, and promptly take corrective actions.
Evaluate the effectiveness of crisis management strategies and make necessary adjustments to improve resilience.
7. Training and Skill Development
Ensure that employees involved in supply chain management have the necessary knowledge and skills to handle crises.
Provide regular training sessions and simulate crisis scenarios to enhance their preparedness and response capabilities.
8. Contingency Planning
Develop contingency plans that outline specific actions to be taken during different crisis scenarios.
These plans should include detailed steps, responsibilities, and communication protocols to minimize confusion and ensure a coordinated response.
9. Stakeholder Engagement
Engage with key stakeholders, such as government agencies, industry associations, and local communities, to foster collaboration and support in times of crisis.
Maintain open lines of communication and establish partnerships to leverage collective resources and expertise.
10. Post-Crisis Analysis
Conduct post-crisis analysis to evaluate the effectiveness of the response and identify areas for improvement.
Learn from past experiences and incorporate lessons into future crisis management strategies.
In fact, effective supply chain crisis management is crucial for ensuring the resilience and continuity of operations in the face of disruptions.
By implementing various key components, businesses can proactively mitigate risks and minimize the negative impact of crises on their supply chain networks.
Boost Your Career with a Standout LinkedIn Profile
Attract recruiters and expand your network with a fully optimized LinkedIn profile tailored to highlight your strengths and professional goals. Let your profile open doors to new opportunities!
Get OptimizedRead: NZ’s Global Logistics: A Manager’s Role
Challenges and Risks in Supply Chain Crisis Management in New Zealand
Supply chain crisis management in New Zealand faces unique challenges and risks.
These include the impact of natural disasters, geopolitical instability, and global disruptions on the supply chain.
Let’s explore these challenges and risks in more detail.
Unique Challenges and Risks Faced by New Zealand in Supply Chain Crisis Management
- New Zealand’s geographical location poses challenges in terms of connectivity with the rest of the world.
- The country’s relatively small population and market size make it more vulnerable to supply chain disruptions.
- High dependence on imports, especially for essential goods, exposes New Zealand to risks in global supply chains.
- The country’s reliance on primary industries, such as agriculture and forestry, exposes it to the impact of natural disasters.
- Complex regulatory frameworks and compliance requirements can create challenges in supply chain crisis management.
Impact of Natural Disasters, Geopolitical Instability, and Global Disruptions on the Supply Chain in New Zealand
- Natural disasters like earthquakes, volcanic eruptions, and floods can severely disrupt transportation routes and infrastructure.
- Geopolitical instability in certain regions can lead to political and trade disruptions, affecting New Zealand’s supply chain.
- Global disruptions, such as pandemics or economic recessions, can have ripple effects on New Zealand’s supply chain.
- Disruptions in key trading partners can lead to supply chain bottlenecks and delays in receiving essential goods.
- The country’s heavy reliance on international shipping can make it vulnerable to disruptions in global maritime trade.
Addressing these challenges
Addressing these challenges and mitigating risks is crucial for effective supply chain crisis management in New Zealand.
Strategies should focus on:
- Diversifying supply sources to reduce dependence on specific regions or countries.
- Improving infrastructure resilience to minimize the impact of natural disasters on transportation networks.
- Enhancing collaboration between the public and private sectors to develop efficient crisis response plans.
- Investing in technologies like real-time tracking and data analytics to monitor and predict supply chain disruptions.
- Creating contingency plans to manage the impact of global disruptions on the supply chain.
Additionally, continuous evaluation and reassessment of supply chain strategies and risk management frameworks is essential to adapt to evolving challenges.
Regular scenario planning exercises can help identify potential vulnerabilities and develop proactive measures.
In short, supply chain crisis management in New Zealand is confronted with unique challenges and risks arising from the country’s geographical location, market size, and primary industries.
Natural disasters, geopolitical instability, and global disruptions also pose significant threats to the supply chain.
By understanding and addressing these challenges, implementing proactive strategies, and investing in resilient infrastructure and technologies, New Zealand can enhance its ability to manage and mitigate supply chain crises.
Read: Effective Inventory Mgmt in NZ
Strategies for Effective Supply Chain Crisis Management in New Zealand
In recent years, the world has witnessed several major supply chain disruptions that have had a significant impact on businesses and economies.
New Zealand, being heavily reliant on international trade and imports, is not immune to such disruptions.
To effectively manage supply chain crises, it is crucial for businesses in New Zealand to adopt proactive strategies that prioritize collaboration, risk assessment, and technology utilization.
Collaboration and Coordination Among Supply Chain Stakeholders
One of the key strategies for effective supply chain crisis management in New Zealand is promoting collaboration and coordination among all stakeholders.
This includes suppliers, manufacturers, distributors, retailers, and even government agencies.
By fostering open communication channels, sharing information, and working together towards a common goal, supply chain partners can better prepare for and respond to crises.
For example, during the COVID-19 pandemic, collaboration between government agencies and businesses played a vital role in ensuring the continued flow of essential goods.
Implementing Robust Risk Assessment and Contingency Planning
Another essential strategy is the implementation of robust risk assessment and contingency planning processes.
This involves identifying potential risks and vulnerabilities in the supply chain, developing proactive mitigation strategies, and establishing alternative routes or sources of supply.
By regularly assessing risks and having contingency plans in place, businesses in New Zealand can minimize the impact of disruptions and quickly adapt to changing circumstances.
Effective risk assessment and contingency planning also reduce the likelihood of supply chain crises or enable prompt responses when they occur.
Utilizing Technology and Data Analytics to Enhance Supply Chain Visibility and Agility
Advancements in technology and data analytics offer significant opportunities to enhance supply chain visibility and agility.
By implementing digital solutions such as cloud-based platforms, real-time tracking systems, and predictive analytics, businesses in New Zealand can gain better insights into their supply chain operations.
This enables proactive monitoring of key performance indicators, early identification of potential bottlenecks, and timely decision-making in the face of crises.
Additionally, technology-driven supply chain solutions improve overall efficiency, reduce costs, and enable businesses to respond swiftly to disruptions.
In general, effective supply chain crisis management in New Zealand requires the adoption of proactive strategies that prioritize collaboration, robust risk assessment, and technology utilization.
By promoting collaboration and coordination among supply chain stakeholders, implementing robust risk assessment and contingency planning processes, and leveraging technology and data analytics, businesses can enhance their ability to navigate and recover from supply chain disruptions.
Embracing these strategies will not only help mitigate the impact of crises but also foster greater resilience and competitiveness in New Zealand’s supply chain ecosystem.
Read: AI & Automation in NZ’s Supply Chains
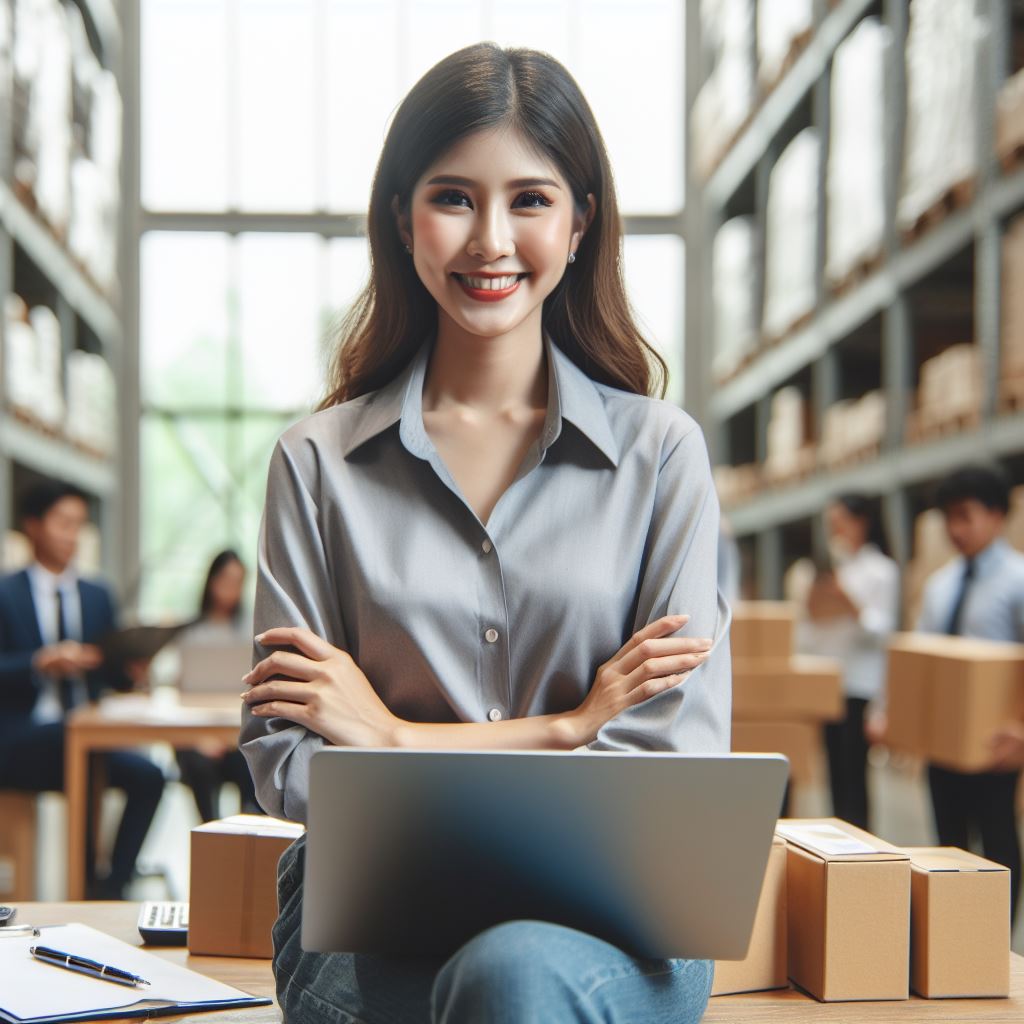
Case Studies: Supply Chain Crisis Management in New Zealand
Supply chain crises can have a significant impact on businesses, economies, and society as a whole.
In New Zealand, there have been notable supply chain crises over the years that have tested the crisis management capabilities of organizations.
This section will examine some of these crises and analyze the strategies that were implemented, both successful and unsuccessful, to manage these crises.
Examination of Notable Supply Chain Crises in New Zealand
- The Rena Oil Spill: In 2011, the cargo ship Rena ran aground off the coast of Tauranga, causing one of New Zealand’s biggest environmental disasters.
The spill had a significant impact on the local marine ecosystem, resulting in the deaths of birds and marine life. - Christchurch Earthquakes: The series of earthquakes that struck Christchurch in 2010 and 2011 disrupted the supply chains in the region.
Buildings and infrastructure were severely damaged, leading to disruptions in transportation and logistics networks. - Pacific Fibre Cable Cut: In 2012, the Pacific Fibre cable connecting New Zealand to the rest of the world was cut, causing a major disruption to internet services.
Businesses and individuals faced significant challenges in communicating and accessing online resources.
Successful and Unsuccessful Crisis Management Strategies
During these supply chain crises, organizations implemented various crisis management strategies.
Some of these strategies were successful and helped mitigate the impact of the crises, while others were ineffective.
Successful Crisis Management Strategies
- Proactive Communication: Organizations that effectively communicated with stakeholders and the public were able to maintain trust and transparency.
This helped in managing public perception and minimizing reputational damage. - Collaboration and Coordination: Successful crisis management involved close collaboration and coordination between various stakeholders, including government agencies, businesses, and community organizations.
Working together helped in efficient resource allocation and timely response. - Resilient Supply Chains: Organizations that had resilient supply chains were better equipped to respond to disruptions.
They had contingency plans in place, alternative suppliers, and robust risk management practices. This ensured a smoother recovery process.
Unsuccessful Crisis Management Strategies
- Lack of Preemptive Planning: Some organizations failed to have preemptive crisis management plans in place, making them ill-prepared to respond to the crises.
This resulted in delays, confusion, and increased damage to their operations and reputation. - Poor Communication and Coordination: Organizations that failed to communicate effectively during the crises experienced greater challenges in managing the perception of stakeholders.
Lack of coordination between different agencies and organizations led to delays in response and inadequate resource allocation. - Overreliance on Single Suppliers or Routes: Organizations that heavily relied on single suppliers or transportation routes were severely impacted when disruptions occurred.
Lack of flexibility and redundancy in their supply chains led to prolonged recovery periods and increased costs.
In review, supply chain crises in New Zealand have highlighted the importance of effective crisis management strategies.
Proactive communication, collaboration, and resilient supply chains have been key factors in successfully managing these crises.
On the other hand, a lack of preemptive planning, poor communication, and overreliance on single suppliers have proven to be ineffective strategies.
Organizations can learn valuable lessons from these case studies and strengthen their crisis management capabilities to navigate future crises more effectively.
Read: Supply Chain Risks & Solutions in NZ
Best Practices for Supply Chain Crisis Management in New Zealand
In order to effectively manage supply chain crises in New Zealand, certain best practices must be followed.
These practices focus on proactive communication, timely decision-making, training and development of crisis management teams, and integration of sustainability and resilience.
Importance of Proactive Communication and Timely Decision-Making
Proactive communication plays a crucial role in managing supply chain crises in New Zealand.
Companies must establish effective communication channels with their suppliers, customers, and other relevant stakeholders.
This includes keeping them informed about the situation, potential risks, and mitigation strategies.
Timely decision-making is equally important in crisis management.
Supply chain managers need to analyze the situation quickly, gather relevant information, and make informed decisions.
This helps in minimizing the impact of the crisis and restoring normalcy as soon as possible.
Training and Development of Crisis Management Teams
In order to effectively handle supply chain crises, companies in New Zealand should invest in training and development of their crisis management teams.
These teams should be equipped with the necessary skills and knowledge to analyze, strategize, and execute crisis response plans.
Regular training exercises should be conducted to simulate different crisis scenarios and test the team’s preparedness.
This helps in identifying gaps and areas that need improvement, allowing for continuous learning and refinement of crisis management strategies.
Integration of Sustainability and Resilience in Supply Chain Crisis Management
Supply chain crisis management in New Zealand should not only focus on mitigating immediate risks but also on long-term sustainability and resilience.
Companies should implement practices that minimize their environmental impact and enhance their ability to adapt to future disruptions.
This can be achieved by diversifying supplier sources, implementing sustainable transportation practices, and adopting technologies that improve supply chain visibility and traceability.
Additionally, companies should collaborate with their suppliers to ensure ethical and socially responsible practices throughout the supply chain.
By integrating sustainability and resilience in supply chain crisis management, companies in New Zealand can not only mitigate the impact of crises but also create a stronger and more sustainable supply chain.
Effective supply chain crisis management in New Zealand requires a proactive approach, timely decision-making, well-trained crisis management teams, and integration of sustainability and resilience.
By following these best practices, companies can minimize the impact of crises and build a more robust and sustainable supply chain.
Government Initiatives and Support for Supply Chain Crisis Management in New Zealand
In recent years, New Zealand has faced a number of supply chain disruptions, ranging from earthquakes to global pandemics like the COVID-19 crisis.
In light of these challenges, the government has implemented various policies, regulations, and initiatives aimed at enhancing supply chain resilience.
Overview of Government Policies, Regulations, and Initiatives
- Supply Chain Resilience Framework: The government has developed a comprehensive framework to guide supply chain resilience planning and management.
- Collaboration with Industry: The government actively collaborates with industry stakeholders to identify risks and develop strategies to mitigate them.
- Investment in Infrastructure: The government has allocated significant funds to improve transportation networks, including ports and roads, to enhance the efficiency and reliability of supply chains.
- Creation of Supply Chain Councils: The government has established councils comprising industry experts to advise on supply chain management and crisis response.
- Regulatory Flexibility: The government has implemented regulatory measures that allow for flexibility during crises, such as streamlined customs procedures and temporary waivers on certain regulations.
Role of Government Agencies in Supporting Supply Chain Crisis Management
- New Zealand Customs Service: The Customs Service plays a crucial role in facilitating the smooth flow of goods across borders during a crisis by implementing efficient clearance processes.
- Ministry of Business, Innovation and Employment (MBIE): MBIE provides support and guidance to businesses affected by supply chain disruptions, helping them navigate challenges and access necessary resources.
- Ministry of Transport: The Ministry of Transport is responsible for developing policies and regulations that ensure the safety and reliability of transportation infrastructure, critical for smooth supply chain operations.
- Ministry for Primary Industries: This ministry focuses on ensuring the resilience of New Zealand’s primary industries, including agriculture and fisheries, by implementing measures to address supply chain challenges specific to these sectors.
- Civil Defence and Emergency Management: This agency collaborates with government agencies and local communities to develop robust emergency response plans and coordinate efforts during crises affecting supply chains.
Impact of government support
The government’s initiatives and support for supply chain crisis management in New Zealand reflect its commitment to building a resilient and adaptive supply chain ecosystem.
By actively collaborating with industry stakeholders and investing in infrastructure and regulatory flexibility, the government aims to minimize the impact of disruptions and ensure the continuity of essential supplies.
However, it is important to acknowledge that supply chain crises are unpredictable and multifaceted.
While government initiatives provide a framework and support, businesses must also take proactive measures to strengthen their own supply chain resilience.
This includes diversifying suppliers, implementing risk management strategies, and leveraging technology to enhance visibility and coordination.
In a nutshell, the New Zealand government’s efforts in supporting supply chain crisis management are commendable.
Through a combination of policies, regulations, and agency support, the government aims to enhance supply chain resilience and minimize the impact of disruptions on businesses and communities.
Moving forward, continued collaboration between the government and industry stakeholders will be crucial in navigating future supply chain challenges effectively.
Conclusion
In this blog post, we discussed key points regarding supply chain crisis management in New Zealand.
We emphasized the importance of continuous improvement in this area.
Throughout the post, we explored the challenges that can arise in supply chain management, including disruptions caused by natural disasters, global events, and other unforeseen circumstances.
We also highlighted the impact these crises can have on New Zealand’s economy and the need for effective crisis management strategies.
We outlined some of the key steps that organizations can take to improve their supply chain crisis management, such as conducting risk assessments, developing robust contingency plans, and enhancing communication and collaboration with suppliers and stakeholders.
Furthermore, we emphasized the importance of proactive measures, such as investing in technologies that can provide real-time monitoring and analysis of supply chain operations, enabling organizations to detect and respond to potential disruptions before they escalate into full-blown crises.
Lastly, we underlined the significance of continuous improvement in supply chain crisis management.
It is essential for organizations to regularly review and update their crisis management plans, learn from past experiences, and invest in training and development to build resilience and agility.
Supply chain crisis management is an ongoing process that requires proactive measures, effective planning, and continuous improvement.
Organizations in New Zealand must recognize the importance of addressing this critical aspect of their operations to mitigate risks and protect their supply chains from potential disruptions.