Introduction
Welding techniques hold a pivotal role within New Zealand’s industrial landscape, spanning vital sectors such as construction and manufacturing.
These techniques serve as the backbone for fabricating structures, machinery, and various components essential for infrastructure development and industrial production.
In the intricate tapestry of construction, welding emerges as a cornerstone, binding together diverse materials to form robust and resilient structures.
From towering skyscrapers to intricate architectural marvels, welding techniques enable the realization of ambitious designs while ensuring structural integrity and safety standards are met.
Similarly, in the realm of manufacturing, welding serves as a linchpin in the production process, facilitating the assembly of intricate machinery, equipment, and components with precision and reliability.
Among the plethora of welding methods available, two techniques stand out prominently: MIG (Metal Inert Gas) and TIG (Tungsten Inert Gas) welding.
These techniques have garnered widespread acclaim for their versatility, efficiency, and ability to produce high-quality welds across a spectrum of materials and thicknesses.
MIG welding, characterized by its simplicity and speed, finds extensive application in industries where rapid and continuous welding is required, such as automotive manufacturing and fabrication workshops.
On the other hand, TIG welding, renowned for its precision and aesthetic appeal, is favored in industries demanding immaculate welds with minimal distortion, such as aerospace and nuclear engineering.
In essence, the significance of welding techniques in New Zealand transcends mere fabrication processes; it underpins the very fabric of modern infrastructure and industrial progress.
To ensure economic progress, we must grasp and utilize MIG and TIG welding techniques effectively.
Read: Kiwi Carpenter Salary Insights 2024
MIG Welding
MIG welding, also known as Metal Inert Gas welding, is a popular welding technique used in New Zealand.
It offers several advantages and finds applications in various industries. Let’s take a closer look at MIG welding and its characteristics.
MIG Welding (Metal Inert Gas)
MIG welding is a process where an electric arc is created between a consumable wire electrode and the workpiece.
This arc melts the wire, which acts as a filler material, creating a strong bond between the two surfaces.
The Process of MIG Welding
MIG welding works by feeding a continuous wire electrode into the welding gun. The electrode then melts and combines with the workpiece, forming a weld joint.
To protect the molten metal from atmospheric contamination, an inert gas shield, such as argon or helium, is used.
The Advantages of MIG Welding
MIG welding offers several advantages that make it a preferred choice for many applications in New Zealand:
- Versatility: MIG welding can be used on a wide range of metals, including stainless steel, aluminum, and mild steel. This versatility makes it a versatile choice for various industries.
- Speed: MIG welding allows for fast deposition rates, making it suitable for high-volume production work.
- Ease of Use: MIG welding is relatively easier to learn and operate compared to other welding techniques, making it accessible to both professionals and beginners.
- Minimal Cleanup: As MIG welding uses a wire electrode, there is no need for flux or slag removal, reducing post-weld cleanup time.
Examples of Industries where MIG Welding is Commonly Used in New Zealand
MIG welding finds extensive applications in various industries in New Zealand, including:
- Automotive: MIG welding is widely used in the automotive industry for fabricating car frames, exhaust systems, and body panels.
- Construction: MIG welding is utilized for joining structural components, such as beams, columns, and steel frames, in the construction industry.
- Fabrication: MIG welding is commonly employed in metal fabrication shops to create a wide range of products, including gates, fences, and metal furniture.
- Shipbuilding: MIG welding is integral to shipbuilding processes, including the fabrication of hulls, decks, and various internal structures.
Potential Limitations or Drawbacks of MIG Welding Techniques
While MIG welding has numerous advantages, it also has some limitations that need to be considered:
- Surface Cleanliness: MIG welding requires a clean and well-prepared surface to ensure a strong and reliable weld. Contaminants or impurities can impact weld quality.
- Outdoor Limitations: Wind or drafts can disperse the shielding gas, leading to porosity or incomplete fusion in the weld. MIG welding is best suited for indoor environments.
- Equipment Cost: MIG welding machines can be more expensive compared to other welding equipment, making it a significant investment for some individuals or businesses.
In short, MIG welding is a versatile and widely used welding technique in New Zealand. It offers many advantages, including its versatility, speed, and ease of use.
However, it is essential to consider its limitations and potential drawbacks for successful application.
Understanding the characteristics and capabilities of MIG welding can help in selecting the right technique for specific welding projects.
Read: Carpentry 101: A Guide for Kiwi Beginners
TIG Welding
Definining TIG welding (Tungsten Inert Gas)
TIG welding, also known as Tungsten Inert Gas welding, is a precise and versatile welding technique commonly used in New Zealand.
It involves using a non-consumable tungsten electrode and an inert gas shield to join different metals together.
The process of TIG welding
The process of TIG welding begins with preparing the metal surfaces to be joined by cleaning them thoroughly.
This ensures a strong and clean weld.
The non-consumable tungsten electrode is then used to create an arc that generates intense heat.
While the electrode does not melt during the process, it plays a crucial role in facilitating the arc and delivering heat to the workpiece.
The inert gas shield, often argon or helium, is used to protect the weld area from oxidation and contamination.
The advantages of TIG welding
One of the main advantages of TIG welding is its precision.
The welder has better control over the process, allowing them to create intricate and accurate welds.
This precision makes TIG welding suitable for applications that require fine detail and high-quality welds, such as aerospace and automotive industries.
Furthermore, TIG welding can join a wide range of metals, including stainless steel, aluminum, and copper.
This versatility makes it a preferred choice for fabricating products that require the joining of dissimilar metals.
TIG welding also offers excellent control over the heat input, minimizing the potential for distortion and ensuring the integrity of the welded joint.
The weld pool can be manipulated easily, allowing for precise control over the penetration and fusion of the metals being joined.
Examples of industries where TIG welding is commonly used
In industries like marine construction and food processing, where hygiene and cleanliness are critical, TIG welding is commonly used due to its ability to produce clean and aesthetically pleasing welds.
The absence of slag or spatter makes post-weld cleanup easier.
Despite its many advantages, TIG welding does have some limitations.
One of the drawbacks is its relatively slower welding speed compared to other techniques.
The slower speed can increase labor costs and production time, making it less efficient for large-scale projects.
Potential limitations or drawbacks of TIG welding techniques
Another limitation of TIG welding is that it requires a higher level of skill and experience to perform correctly.
The precise control and attention to detail needed may take time to master, leading to increased training and certification requirements for welders.
In fact, TIG welding is a versatile and precise welding technique commonly used in various industries in New Zealand.
Its ability to weld different metals, excellent control, and clean welds make it a preferred choice for applications that require high-quality welding.
However, the slower welding speed and need for skilled welders can pose some limitations.
Personalized Career Consulting
Unlock your potential with expert career advice tailored to your goals. Get personalized guidance and actionable steps toward your dream career in New Zealand.
Get StartedRead: Top Carpentry Courses in New Zealand
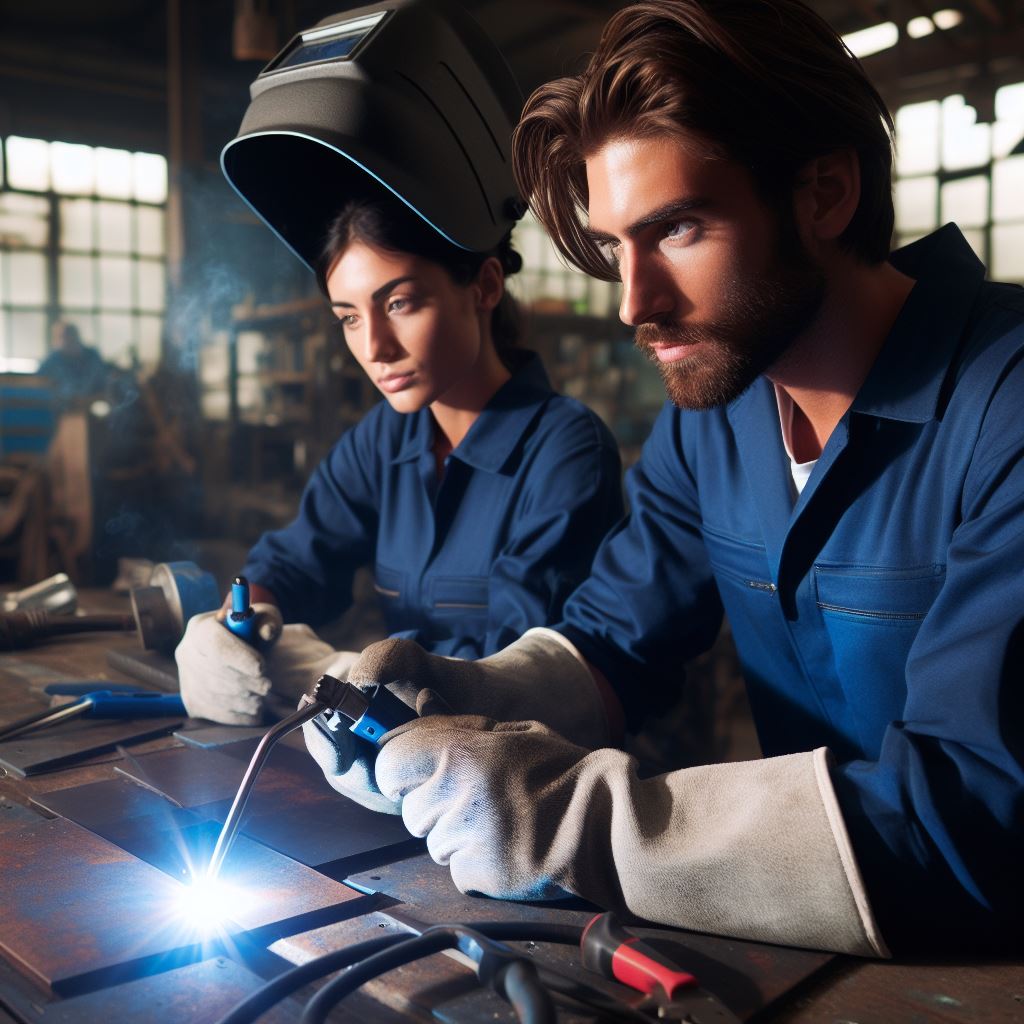
Comparison between MIG and TIG Welding
When it comes to welding techniques, MIG (Metal Inert Gas) and TIG (Tungsten Inert Gas) are two popular methods used in New Zealand.
While both techniques can produce high-quality welds, there are significant differences between them that make each suitable for specific applications.
In this section, we will highlight the key differences between MIG and TIG welding techniques, including the nature of the welding process, equipment used, and the types of joints they are best suited for.
The Nature of the Welding Process
MIG welding utilizes a consumable wire electrode that continuously feeds through a gun.
The wire melts, creating the arc that joins the workpieces together.
It is a faster process that allows for higher deposition rates and is often used for thicker materials.
On the other hand, TIG welding uses a non-consumable tungsten electrode to create the arc.
The filler material is added separately, and the process requires more skill and precision.
Equipment Used
For MIG welding, a power source, a wire feeder, and a welding gun are required.
The wire feeder controls the speed at which the electrode is fed, while the gun directs the wire and shielding gas to the weld pool.
TIG welding, on the other hand, requires a power source, a TIG torch, and a separate filler material.
The TIG torch delivers the current and shielding gas, while the welder manually adds the filler rod.
Types of Joints
MIG welding is best suited for joining large, straight welds or curved welds.
It is commonly used for welding joints that require high production rates, such as in automotive and manufacturing industries.
TIG welding, on the other hand, is ideal for welding thin materials or complicated joints. It provides precise control over the heat input and produces clean and aesthetically pleasing welds.
It is commonly used in aerospace, art, and jewelry industries.
Factors that Influence the Choice
Several factors come into play when choosing between MIG and TIG welding.
The type of material being welded is crucial as MIG welding works well on steel, stainless steel, and aluminum, while TIG welding works on a broader range of materials, including non-ferrous metals.
Joint complexity is another consideration; MIG welding is suitable for simpler joints, while TIG welding excels in complex and intricate joints.
Lastly, project requirements, such as strength, appearance, and budget, also influence the choice.
Examples of Suitable Scenarios
- MIG welding is ideal for fabricating structural components, such as beams and frames, in the construction industry.
- TIG welding is well-suited for creating precise and appealing welds on sculptures or artwork.
- When working with thin materials, like sheet metal, TIG welding ensures minimal distortion and warping.
- For automotive repair, MIG welding is commonly used to join body panels and framework due to its speed and efficiency.
Cost Considerations
When trying to choose between MIG and TIG welding methods, cost is a significant factor.
MIG welding is generally less expensive as it requires fewer tools and less skill.
TIG welding, on the other hand, demands a higher cost due to the need for specialized equipment and skilled welders.
Additionally, TIG welding often involves additional steps like cleaning and prepping, which can increase the overall project cost.
In general, both MIG and TIG welding techniques have their own advantages and areas of specialization.
To ensure successful welding projects in New Zealand, consider factors like material type, joint complexity, and project requirements to make the right choice.
Read: NZ Carpentry: Skills and Tools Needed
Conclusion
MIG and TIG welding techniques have been discussed in the context of New Zealand.
This section highlighted the key differences between the two methods, including their use of different electrode types, heat sources, and levels of skill required.
Both MIG and TIG welding techniques have their advantages and disadvantages.
MIG welding is known for its speed and ease of use, making it suitable for large-scale projects with thick materials.
On the other hand, TIG welding offers superior precision and control, making it ideal for intricate projects and thin materials.
It is essential to choose the appropriate welding technique based on project requirements and desired outcomes.
Selecting the wrong technique can lead to compromised weld quality and increased project costs.
Therefore, it is crucial to consider factors such as material type, thickness, and welding location.
As the welding industry in New Zealand continues to evolve, it is important to stay updated with the latest advancements, regulations, and safety guidelines.
Furthermore, considering the unique environmental conditions and specific project requirements in New Zealand will help ensure successful welding outcomes.
To further explore the field of welding, readers are encouraged to research additional factors that are specific to New Zealand’s welding industry.
This may include understanding local welding certifications, industry standards, and available welding technologies.
Welders in New Zealand can achieve high-quality welds and contribute to industries by using proper techniques and training.