Introduction
Mechanics play a vital role in ensuring the proper functioning of vehicles.
They are responsible for repairs, maintenance, and inspections.
However, their job can be hazardous, making mechanic health and safety a top priority in New Zealand.
Ensuring the health and safety of mechanics is important for several reasons.
Firstly, it protects the well-being of the workers, preventing accidents and injuries that could have severe consequences.
Secondly, maintaining a safe working environment contributes to overall productivity and efficiency in the industry.
This blog post will provide an overview of the standards set by the New Zealand government regarding mechanic health and safety.
These standards cover various aspects, including hazard identification, risk assessment, and safety training.
Adhering to these standards is crucial to create a safe working environment for mechanics.
It will also discuss helpful tips for mechanics to maintain their health and safety.
These include wearing appropriate protective equipment, following proper handling procedures for hazardous substances, and maintaining a clean and organized workspace.
In review, mechanic health and safety is of utmost importance in New Zealand.
By adhering to the NZ standards and implementing best practices, we can protect the well-being of mechanics and ensure a safe working environment.
Stay tuned for the upcoming sections of this blog post, where we will delve deeper into each aspect of mechanic health and safety.
New Zealand Health and Safety at Work Act (2015)
Overview of the Act
The New Zealand Health and Safety at Work Act emphasizes the importance of creating a safe working environment for mechanics.
By implementing these key provisions, the Act aims to reduce accidents, injuries, and fatalities in the industry.
Under the Act, mechanics have a duty of care to ensure their own safety and that of their co-workers, customers, and the general public.
This obligation extends to taking precautions to prevent accidents and using appropriate safety equipment.
Key provisions related to mechanic health and safety
Worker engagement and participation play a crucial role in improving health and safety practices.
Mechanics should be actively involved in identifying potential hazards and suggesting ways to mitigate risks.
Employers must encourage open communication and provide support for workers to report safety concerns.
Hazard identification and risk management are essential for minimizing workplace accidents.
Employers and employees need to continually assess and address potential hazards, such as working with hazardous substances or operating heavy machinery.
Adequate training and supervision are necessary to equip mechanics with the knowledge and skills to perform their tasks safely.
Employers have a responsibility to provide initial and ongoing training, as well as ensuring that supervisors are capable of overseeing work processes effectively.
Incident reporting and investigation help identify underlying causes and prevent future accidents.
Mechanic-related incidents, whether resulting in injury, damage, or near misses, must be reported promptly.
A thorough investigation should follow to determine contributing factors and implement preventative measures.
The Act’s enforcement measures and penalties serve as deterrents to non-compliance.
Employers and workers should be aware of their respective obligations and the potential consequences of failing to meet health and safety standards.
In review, the New Zealand Health and Safety at Work Act outlines key provisions that are relevant to ensuring the health and safety of mechanics.
By understanding and implementing these provisions, employers, employees, and regulators can work together to create a safer working environment in the automotive industry.
Mechanic Health and Safety Regulations in New Zealand
The regulations specific to the mechanic industry
Workplace layout and organization
In order to ensure the health and safety of mechanics in New Zealand, specific regulations have been put in place to ensure proper workplace layout and organization.
These regulations ensure that the workspaces are properly designed and set up, allowing for safe and efficient work practices.
Mechanical and electrical equipment safety
Another important aspect of mechanic health and safety in New Zealand is the regulations surrounding the safety of mechanical and electrical equipment.
These regulations ensure that all equipment used in the mechanic industry is well-maintained and regularly inspected to prevent accidents and injuries.
Hazardous substances management
The mechanic industry often deals with hazardous substances such as lubricants, fuels, and cleaning agents.
To protect the health of mechanics, New Zealand has strict regulations on the management of hazardous substances, including proper storage, handling, and disposal procedures.
Personal protective equipment requirements
Personal protective equipment (PPE) is crucial in providing a safe working environment for mechanics.
New Zealand regulations specify the type of PPE that mechanics should wear, such as safety goggles, gloves, and protective clothing, to protect them from potential hazards.
Hazardous manual tasks guidelines
Performing manual tasks can pose risks for mechanics’ health and safety.
To prevent musculoskeletal disorders and other injuries, New Zealand has developed guidelines for hazardous manual tasks, including proper training, equipment use, and ergonomics, to minimize risks.
Noise control and hearing conservation
Noise is a common hazard for mechanics due to the use of power tools and machinery.
New Zealand regulations require employers to implement noise control measures, such as soundproofing and providing hearing protection, to protect mechanics from hearing loss and other auditory health issues.
Working at heights safety measures
Working at heights is sometimes required in the mechanic industry.
To ensure the safety of mechanics, New Zealand has regulations in place to address the risks associated with working at heights, including the use of appropriate fall protection equipment and proper training.
Safe handling and storage of tools
Tools are essential in the mechanic industry, but they can also pose hazards if not handled and stored properly.
New Zealand regulations require mechanics to follow safe practices when handling tools, including proper storage, regular maintenance, and training to prevent accidents and injuries.
In fact, the mechanic industry in New Zealand is subject to specific health and safety regulations to protect the well-being of mechanics.
These regulations cover various aspects, including workplace organization, equipment safety, hazardous substances management, personal protective equipment, manual task guidelines, noise control, working at heights safety, and tool handling.
Compliance with these regulations is vital to ensure a safe working environment and prevent accidents and injuries in the mechanic industry.
Read: Top Carpentry Courses in New Zealand
Common Workplace Hazards for Mechanics
Potential hazards in a mechanic workshop
- Poor indoor air quality due to chemicals and exhaust fumes.
- Noise pollution from running engines, power tools, and pneumatic machines.
- Inadequate lighting resulting in poor visibility and increased risk of accidents.
- Presence of flammable substances like gasoline, oil, and solvents.
- Exposure to toxic substances, including asbestos, lead, and silica.
- Physical strains and injuries from lifting heavy objects and performing repetitive tasks.
Risks associated with each hazard
- Poor indoor air quality can lead to respiratory problems and long-term health issues.
- Noise pollution can cause hearing loss, stress, and difficulty in communication.
- Inadequate lighting increases the chances of slips, trips, and falls.
- Flammable substances can result in fires, explosions, and severe injuries.
- Exposure to toxic substances may cause poisoning, cancer, or other chronic illnesses.
- Physical strains and injuries can lead to musculoskeletal disorders and reduced productivity.
Strategies for hazard identification and control
- Regular inspections and risk assessments to identify potential risks and hazards.
- Implementing safety protocols and procedures to minimize risks and ensure safe working practices.
- Providing proper training and supervision to workers to enhance their awareness and competence.
- Using safety equipment and protective measures, such as goggles, masks, gloves, and footwear.
Mechanics conduct regular inspections, identify hazards, and control risks to ensure a safe workplace.
Inspections cover ventilation, noise, lighting, and storage, involving workers for insights and active participation.
Personalized Career Consulting
Unlock your potential with expert career advice tailored to your goals. Get personalized guidance and actionable steps toward your dream career in New Zealand.
Get StartedImplement safety protocols for tasks like handling flammable substances, using power tools, and heavy lifting.
Periodically review and update protocols to align with safety standards, training all workers and enforcing consistent implementation.
Comprehensive training on hazard identification, risk assessment, and safe equipment use is essential for mechanics.
Ongoing supervision reinforces safe practices and promptly addresses any concerns.
Mechanics must wear appropriate PPE such as goggles, masks, gloves, and footwear for tasks.
Ensure the workshop has sufficient functional fire extinguishers and firefighting equipment for emergencies.
Implement strategies like inspections, protocols, training, and equipment use to mitigate workplace hazards.
Read: NZ Carpentry: Skills and Tools Needed
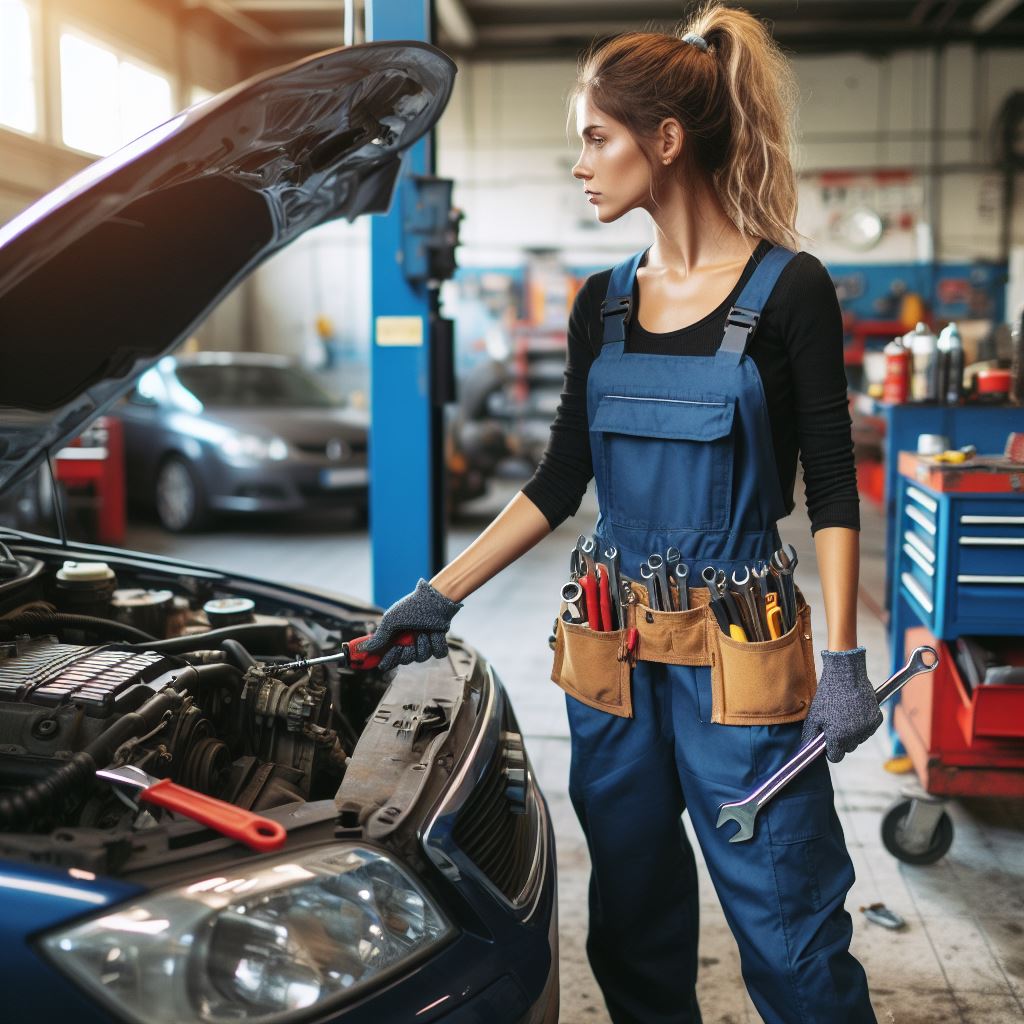
The Role of Employers and Employees in Mechanic Health and Safety
Responsibilities of employers
It is important for both employers and employees to understand and fulfill their respective roles in ensuring mechanic health and safety.
By working together, they can create a conducive and secure work environment.
Employers play a crucial role in providing a safe and healthy workplace for mechanics.
They must establish and maintain policies and procedures that minimize risks and hazards.
Creating a safe and healthy workplace environment involves a range of responsibilities for employers.
They must ensure that the physical workspace is properly maintained, with adequate ventilation, lighting, and equipment.
Additionally, employers must address any potential hazards promptly and take appropriate measures to eliminate or minimize them.
Moreover, it is the employer’s responsibility to provide comprehensive training and supervision to mechanics.
This includes initial training when employees are hired, as well as ongoing training to keep up with changing standards and best practices.
Without proper training, mechanics may be at a higher risk of accidents and injuries.
Engaging workers in health and safety matters is equally important.
Employers should encourage open communication and involve mechanics in developing and implementing safety protocols.
By seeking input and feedback from employees, employers can gain valuable insights and improve the overall safety culture of the workplace.
Reporting and investigating incidents or accidents promptly is a critical step in ensuring mechanic health and safety.
Employers must establish a clear reporting system and encourage employees to report any incidents, no matter how minor they may seem.
Thorough investigations should be conducted to identify the root causes of accidents and take preventive measures to avoid similar incidents in the future.
While employers have significant responsibilities, employees also play a vital role in maintaining a safe working environment.
Employees must always adhere to safety rules and procedures, as these are in place to protect themselves and their colleagues.
By following these guidelines, mechanics can minimize the risk of accidents and injuries.
Responsibilities of employees
Employees should actively participate in health and safety initiatives.
This includes attending safety training sessions, engaging in safety meetings, and actively seeking opportunities to improve their own understanding of health and safety practices.
By taking an active interest in their own well-being and that of their colleagues, employees can contribute to a safer workplace.
Additionally, employees have a responsibility to report any hazards or unsafe conditions they observe in the workplace.
This could include faulty equipment, inadequate PPE, or potential risks that have not been adequately addressed.
Reporting such concerns promptly allows employers to take corrective action and mitigate potential hazards.
Lastly, employees must use personal protective equipment correctly to ensure their own safety.
PPE, such as goggles, gloves, and helmets, should be worn whenever required.
Proper usage of PPE can significantly reduce the risk of injuries and accidents that mechanics may face while working.
In a nutshell, both employers and employees play crucial roles in maintaining mechanic health and safety.
Employers must provide a safe and healthy workplace environment, implement safety policies, provide training, and engage workers in health and safety matters.
Employees, on the other hand, must follow safety rules, report hazards, participate in health and safety initiatives, and use personal protective equipment correctly.
By actively fulfilling their respective responsibilities, employers and employees can work together to prioritize and maintain a safe working environment for mechanics.
Read: Carpenter Apprenticeships in NZ Explained
Resources and Support for Mechanic Health and Safety
Government agencies and organizations offering assistance
Mechanics can rely on government agencies like the Occupational Safety and Health Service for support and advice.
They provide resources such as guidelines, training programs, and consultations to promote a safe working environment.
These organizations emphasize the importance of compliance with health and safety regulations to mitigate workplace hazards.
By partnering with government agencies, mechanics can benefit from expert knowledge and access to specialized assistance.
Having these resources readily available can enhance the overall health and safety practices within the industry.
Training programs and certifications for mechanics
Attending training programs and acquiring certifications play a crucial role in ensuring mechanic health and safety.
Mechanics can enroll in courses that focus on topics such as hazard identification, safe work practices, and proper tool usage.
These programs provide valuable insights into implementing safety protocols and staying updated with industry standards.
Certifications validate a mechanic’s competency and demonstrate their commitment to maintaining a safe working environment.
By investing in training and certifications, mechanics can enhance their skills and protect their well-being while on the job.
Online resources and guides on mechanic health and safety
In the digital age, mechanics have access to a plethora of online resources and guides on health and safety.
Websites dedicated to mechanic health and safety offer a wealth of information, including best practices and case studies.
These resources cover various topics such as risk assessment, personal protective equipment, and emergency response protocols.
Mechanics can utilize these online platforms to educate themselves and stay informed about the latest safety measures.
By regularly referencing these resources, they can stay proactive in implementing effective health and safety practices.
Transform Your Career with a Professional CV and Cover Letter
Stand out to employers with an ATS-optimized resume and tailored cover letter designed to match your dream role. Let us craft your job application materials for success!
Get StartedImportance of seeking professional advice and guidance
Mechanics should never underestimate the importance of seeking professional advice and guidance regarding health and safety.
Consulting with experts in the field can provide valuable insights into specific hazards and risk mitigation strategies.
Experienced professionals can conduct workplace assessments, offering personalized advice on improving safety measures.
Furthermore, seeking guidance from industry veterans fosters a culture of continuous improvement in mechanic health and safety.
By actively seeking advice, mechanics can address potential risks and create a safer and more secure working environment.
In summary, mechanics have a wide range of resources and support available to ensure their health and safety.
Government agencies and organizations offer assistance through guidelines, training programs, and consultations.
Training programs and certifications enhance skills and validate a mechanic’s commitment to safety.
Online resources and guides provide easily accessible knowledge to stay informed about best practices.
Seeking professional advice and guidance fosters continuous improvement in mechanic health and safety.
By utilizing these resources and support systems, mechanics can create a working environment that prioritizes their well-being.
Read: Kiwi Carpenter Salary Insights 2024
Conclusion
Recap of key points discussed in the blog post
Throughout this blog post, we have emphasized the importance of mechanic health and safety in New Zealand.
We have discussed the various NZ standards and regulations that mechanics and employers must adhere to in order to ensure a safe and healthy work environment.
Importance of prioritizing mechanic health and safety in New Zealand
The well-being of mechanics should be a top priority for employers as it not only ensures their safety but also promotes productivity and reduces the risk of accidents and injuries.
By adhering to the standards and regulations, employers can create a work environment that fosters employee well-being.
Encouragement for mechanics and employers to adhere to the standards and regulations mentioned
We strongly encourage mechanics and employers to take the necessary steps to comply with the NZ standards and regulations.
By doing so, mechanics can feel confident that their health and safety are being prioritized while employers can mitigate potential risks and liabilities.
Call-to-action
Promote a safe and healthy work environment for all mechanics in New Zealand.
Let us all work together to create a culture of safety and well-being in the mechanic industry in New Zealand.
By promoting and implementing the necessary measures, we can ensure that mechanics have access to a safe and healthy work environment.